ସୋଲଡର ବିଡିଂ ବିଷୟରେ ଆଲୋଚନା କରିବାବେଳେ, ଆମକୁ ପ୍ରଥମେ SMT ତ୍ରୁଟିକୁ ସଠିକ୍ ଭାବରେ ବ୍ୟାଖ୍ୟା କରିବାକୁ ପଡିବ | ଟିଫିନ୍ ବିଡ୍ ଏକ ରିଫ୍ଲୋ ୱେଲଡେଡ୍ ପ୍ଲେଟରେ ମିଳିଥାଏ, ଏବଂ ଆପଣ ଏକ ନଜରରେ କହିପାରିବେ ଯେ ଏହା ଏକ ବୃହତ ଟିଫିନ୍ ବଲ୍ ଯାହା ଫ୍ଲକ୍ସର ପୁଲରେ ଏମ୍ବେଡ୍ ହୋଇଛି ଯାହା ଅତି ନିମ୍ନ ଭୂମି ଉଚ୍ଚତା ବିଶିଷ୍ଟ ପୃଥକ ଉପାଦାନଗୁଡ଼ିକ ପାଖରେ ଅଛି, ଯେପରିକି ସିଟ୍ ପ୍ରତିରୋଧକ ଏବଂ କ୍ୟାପେସିଟର, ପତଳା | ଛୋଟ ପ୍ରୋଫାଇଲ୍ ପ୍ୟାକେଜ୍ (TSOP), ଛୋଟ ପ୍ରୋଫାଇଲ୍ ଟ୍ରାନଜିଷ୍ଟର୍ (SOT), D-PAK ଟ୍ରାନଜିଷ୍ଟର୍, ଏବଂ ପ୍ରତିରୋଧ ଆସେମ୍ବଲି | ଏହି ଉପାଦାନଗୁଡ଼ିକ ସହିତ ସେମାନଙ୍କର ସ୍ଥିତି ହେତୁ, ଟିଫିନ୍ ବିଡ୍ଗୁଡ଼ିକୁ “ଉପଗ୍ରହ” ଭାବରେ କୁହାଯାଏ |
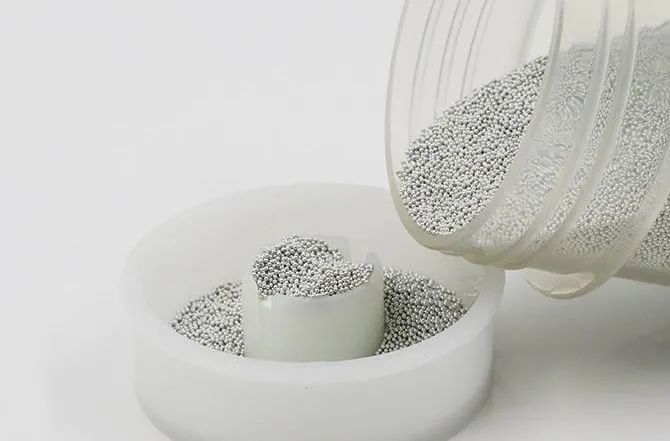
ଟିନ୍ ବିଡ୍ କେବଳ ଉତ୍ପାଦର ରୂପକୁ ପ୍ରଭାବିତ କରେ ନାହିଁ, ଗୁରୁତ୍ୱପୂର୍ଣ୍ଣ କଥା ହେଉଛି, ମୁଦ୍ରିତ ପ୍ଲେଟରେ ଉପାଦାନଗୁଡ଼ିକର ଘନତା ହେତୁ, ବ୍ୟବହାର ସମୟରେ ଲାଇନର ସର୍ଟ ସର୍କିଟ୍ ହେବାର ଆଶଙ୍କା ରହିଥାଏ, ଯାହାଦ୍ୱାରା ଇଲେକ୍ଟ୍ରୋନିକ୍ ଉତ୍ପାଦର ଗୁଣ ପ୍ରଭାବିତ ହୁଏ | ଟିଫିନ୍ ବିଡ୍ ଉତ୍ପାଦନ ପାଇଁ ଅନେକ କାରଣ ଅଛି, ପ୍ରାୟତ one ଏକ ବା ଏକାଧିକ କାରଣରୁ ହୋଇଥାଏ, ତେଣୁ ଏହାକୁ ଭଲ ଭାବରେ ନିୟନ୍ତ୍ରଣ କରିବା ପାଇଁ ଆମକୁ ପ୍ରତିରୋଧ ଏବଂ ଉନ୍ନତିର ଏକ ଭଲ କାମ କରିବାକୁ ପଡିବ | ପରବର୍ତ୍ତୀ ଆର୍ଟିକିଲ୍ ଟିନ୍ ବିଡ୍ ଉତ୍ପାଦନକୁ ପ୍ରଭାବିତ କରୁଥିବା କାରଣଗୁଡିକ ଏବଂ ଟିଫିନ୍ ବିଡ୍ ଉତ୍ପାଦନକୁ ହ୍ରାସ କରିବା ପାଇଁ ପ୍ରତିକ୍ରିୟା ଉପରେ ଆଲୋଚନା କରିବ |
ଟିଣ ବିଡି କାହିଁକି ହୁଏ?
ସରଳ ଭାବରେ କହିବାକୁ ଗଲେ, ଟିଫିନ୍ ବିଡ୍ ସାଧାରଣତ too ଅତ୍ୟଧିକ ସୋଲଡର ପେଷ୍ଟ ଜମା ସହିତ ଜଡିତ ହୋଇଥାଏ, କାରଣ ଏହାର ଏକ “ଶରୀର” ର ଅଭାବ ରହିଥାଏ ଏବଂ ଟିଫିନ୍ ବିଡ୍ ଗଠନ ପାଇଁ ପୃଥକ ଉପାଦାନଗୁଡ଼ିକ ତଳେ ଚାପି ହୋଇ ରହିଥାଏ, ଏବଂ ସେମାନଙ୍କର ଚେହେରାର ବୃଦ୍ଧିକୁ ଧୋଇବା ବ୍ୟବହାରରେ ବୃଦ୍ଧି କରାଯାଇପାରେ | ସୋଲଡର ପେଷ୍ଟରେ | ଯେତେବେଳେ ଚିପ୍ ଉପାଦାନ ଧୋଇବା ଯୋଗ୍ୟ ସୋଲଡର ପେଷ୍ଟରେ ମାଉଣ୍ଟ ହୁଏ, ସୋଲଡର ପେଷ୍ଟ ଉପାଦାନ ତଳେ ଚାପି ହେବାର ସମ୍ଭାବନା ଅଧିକ | ଯେତେବେଳେ ଜମା ହୋଇଥିବା ସୋଲଡର ପେଷ୍ଟ ଅତ୍ୟଧିକ ଥାଏ, ଏକ୍ସଟ୍ରୁଜନ୍ କରିବା ସହଜ ହୋଇଥାଏ |
ଟିଣ ବିଡି ଉତ୍ପାଦନକୁ ପ୍ରଭାବିତ କରୁଥିବା ମୁଖ୍ୟ କାରଣଗୁଡ଼ିକ ହେଉଛି:
(1) ଟେମ୍ପଲେଟ୍ ଖୋଲିବା ଏବଂ ପ୍ୟାଡ୍ ଗ୍ରାଫିକ୍ ଡିଜାଇନ୍ |
(୨) ଟେମ୍ପଲେଟ୍ ସଫା କରିବା |
(3) ଯନ୍ତ୍ରର ପୁନରାବୃତ୍ତି ସଠିକତା |
(4) ରିଫ୍ଲୋ ଫର୍ଣ୍ଣେସର ତାପମାତ୍ରା ବକ୍ର |
(5) ପ୍ୟାଚ୍ ଚାପ |
(6) ପ୍ୟାନ ବାହାରେ ସୋଲଡର ପେଷ୍ଟ ପରିମାଣ |
(7) ଟିଣର ଅବତରଣ ଉଚ୍ଚତା |
(8) ରେଖା ପ୍ଲେଟ୍ ଏବଂ ସୋଲଡର ପ୍ରତିରୋଧ ସ୍ତରରେ ଅସ୍ଥିର ପଦାର୍ଥର ଗ୍ୟାସ୍ ରିଲିଜ୍ |
(9) ଫ୍ଲକ୍ସ ସହିତ ଜଡିତ |
ଟିଣ ବିଡି ଉତ୍ପାଦନକୁ ରୋକିବା ପାଇଁ ଉପାୟ:
(1) ଉପଯୁକ୍ତ ପ୍ୟାଡ୍ ଗ୍ରାଫିକ୍ସ ଏବଂ ସାଇଜ୍ ଡିଜାଇନ୍ ଚୟନ କରନ୍ତୁ | ପ୍ରକୃତ ପ୍ୟାଡ୍ ଡିଜାଇନ୍ରେ, PC ସହିତ ମିଳିତ ହେବା ଉଚିତ, ଏବଂ ତା’ପରେ ପ୍ରକୃତ ଉପାଦାନ ପ୍ୟାକେଜ୍ ଆକାର, ୱେଲଡିଂ ଶେଷ ଆକାର ଅନୁଯାୟୀ, ସଂପୃକ୍ତ ପ୍ୟାଡ୍ ଆକାରକୁ ଡିଜାଇନ୍ କରିବା ଉଚିତ |
()) ଇସ୍ପାତ ଜାଲ ଉତ୍ପାଦନ ଉପରେ ଧ୍ୟାନ ଦିଅନ୍ତୁ | ସୋଲଡର ପେଷ୍ଟର ମୁଦ୍ରଣ ପରିମାଣକୁ ନିୟନ୍ତ୍ରଣ କରିବା ପାଇଁ PCBA ବୋର୍ଡର ନିର୍ଦ୍ଦିଷ୍ଟ ଉପାଦାନ ଲେଆଉଟ୍ ଅନୁଯାୟୀ ଖୋଲିବା ଆକାରକୁ ସଜାଡିବା ଆବଶ୍ୟକ |
()) BGA, QFN ଏବଂ ବୋର୍ଡରେ ଘନ ପାଦ ଉପାଦାନ ସହିତ PCB ଖାଲି ବୋର୍ଡଗୁଡିକ କଠୋର ବେକିଂ କାର୍ଯ୍ୟାନୁଷ୍ଠାନ ଗ୍ରହଣ କରିବାକୁ ପରାମର୍ଶ ଦିଆଯାଇଛି | ୱେଲଡେବିଲିଟି ବ imize ାଇବା ପାଇଁ ସୋଲଡର ପ୍ଲେଟରେ ଥିବା ଭୂପୃଷ୍ଠ ଆର୍ଦ୍ରତାକୁ ଅପସାରଣ କରାଯିବା ନିଶ୍ଚିତ କରିବାକୁ |
(4) ଟେମ୍ପଲେଟ୍ ସଫେଇର ଗୁଣରେ ଉନ୍ନତି କର | ଯଦି ସଫା କରିବା ପରିଷ୍କାର ନୁହେଁ | ଟେମ୍ପଲେଟ୍ ଖୋଲିବା ତଳେ ଥିବା ଅବଶିଷ୍ଟ ସୋଲଡର ପେଷ୍ଟ ଟେମ୍ପଲେଟ୍ ଖୋଲିବା ନିକଟରେ ଜମା ହୋଇ ଅଧିକ ସୋଲଡର ପେଷ୍ଟ ସୃଷ୍ଟି କରିବ, ଯାହାଫଳରେ ଟିଫିନ୍ ବିଡ୍ ସୃଷ୍ଟି ହେବ |
(5) ଯନ୍ତ୍ରର ପୁନରାବୃତ୍ତି ନିଶ୍ଚିତ କରିବାକୁ | ଯେତେବେଳେ ଟେମ୍ପଲେଟ୍ ଏବଂ ପ୍ୟାଡ୍ ମଧ୍ୟରେ ଅଫସେଟ୍ ହେତୁ ସୋଲଡର ପେଷ୍ଟ ପ୍ରିଣ୍ଟ୍ ହୁଏ, ଯଦି ଅଫସେଟ୍ ବହୁତ ବଡ ହୁଏ, ସୋଲଡର ପେଷ୍ଟକୁ ପ୍ୟାଡ୍ ବାହାରେ ଭିଜାଇ ଦିଆଯିବ, ଏବଂ ଗରମ ହେବା ପରେ ଟିଫିନ୍ ବିଡ୍ ସହଜରେ ଦେଖାଯିବ |
(6) ମାଉଣ୍ଟିଂ ମେସିନର ମାଉଣ୍ଟିଂ ଚାପକୁ ନିୟନ୍ତ୍ରଣ କରନ୍ତୁ | ଚାପ ନିୟନ୍ତ୍ରଣ ମୋଡ୍ ସଂଲଗ୍ନ ହୋଇଛି କିମ୍ୱା ଉପାଦାନର ଘନତା ନିୟନ୍ତ୍ରଣ, ଟିଫିନ୍ ବିଡ୍ ରୋକିବା ପାଇଁ ସେଟିଂସମୂହକୁ ସଜାଡିବା ଆବଶ୍ୟକ |
(7) ତାପମାତ୍ରା ବକ୍ରକୁ ଅପ୍ଟିମାଇଜ୍ କରନ୍ତୁ | ରିଫ୍ଲୋ ୱେଲଡିଂର ତାପମାତ୍ରାକୁ ନିୟନ୍ତ୍ରଣ କରନ୍ତୁ, ଯାହା ଦ୍ sol ାରା ଦ୍ରବଣ ଏକ ଉନ୍ନତ ପ୍ଲାଟଫର୍ମରେ ଅସ୍ଥିର ହୋଇପାରିବ |
"ଉପଗ୍ରହ" କୁ ଦେଖ ନାହିଁ ଛୋଟ, ଜଣେ ଟାଣି ହୋଇପାରିବ ନାହିଁ, ସମଗ୍ର ଶରୀରକୁ ଟାଣିବ | ଇଲେକ୍ଟ୍ରୋନିକ୍ସ ସହିତ, ଶୟତାନ ପ୍ରାୟତ the ସବିଶେଷ ତଥ୍ୟରେ ଥାଏ | ତେଣୁ, ପ୍ରକ୍ରିୟା ଉତ୍ପାଦନ କର୍ମଚାରୀଙ୍କ ଧ୍ୟାନ ସହିତ, ସମ୍ପୃକ୍ତ ବିଭାଗଗୁଡିକ ମଧ୍ୟ ସକ୍ରିୟ ଭାବରେ ସହଯୋଗ କରିବା ଉଚିତ ଏବଂ ବସ୍ତୁ ପରିବର୍ତ୍ତନ, ସ୍ଥାନାନ୍ତର ଏବଂ ଅନ୍ୟାନ୍ୟ ବିଷୟ ପାଇଁ ପ୍ରକ୍ରିୟା କର୍ମଚାରୀଙ୍କ ସହିତ ଯୋଗାଯୋଗ କରିବା ଉଚିତ ଯାହାକି ବସ୍ତୁ ପରିବର୍ତ୍ତନ ଦ୍ୱାରା ସୃଷ୍ଟି ହୋଇଥିବା ପ୍ରକ୍ରିୟା ପାରାମିଟରରେ ପରିବର୍ତ୍ତନକୁ ରୋକିବା ପାଇଁ | PCB ସର୍କିଟ୍ ଡିଜାଇନ୍ ପାଇଁ ଦାୟୀ ଡିଜାଇନର୍ ମଧ୍ୟ ପ୍ରୋସେସ୍ କର୍ମଚାରୀଙ୍କ ସହିତ ଯୋଗାଯୋଗ କରିବା, ପ୍ରକ୍ରିୟା କର୍ମଚାରୀଙ୍କ ଦ୍ provided ାରା ପ୍ରଦାନ କରାଯାଇଥିବା ସମସ୍ୟା କିମ୍ବା ପରାମର୍ଶକୁ ଅନୁସରଣ କରିବା ଏବଂ ଯଥାସମ୍ଭବ ଉନ୍ନତି କରିବା ଉଚିତ୍ |
ପୋଷ୍ଟ ସମୟ: ଜାନ -09-2024 |